Roofs: Collapse and Performance Failures
To introduce this topic, it is first important to have the reader understand the terminology of a roof system so as not to confuse it with what is generally referred to as a roof. According to the National Roofing Contractors Association, or NRCA assembly is “a system of interacting roof components including the , vapor retarder (if present), insulation and membrane.” However, a roof is “a system interacting roof components generally consisting of a membrane … and roof insulation (not including the roof deck) designed to weatherproof and sometimes improve the building’s thermal resistance.” Therefore, this article will refer to the structural portion of the assembly as “roof” and the performance, or weatherproofing, portion of the assembly as “roof system” or “roofing”.
A roof that has a low pitch (less than or equal to 25% slope) is referred to as a flat roof or low-sloped roof, and is the most common roof type in commercial construction. There are many different roof system types available for use with the flat roof. The most common among these roofing types are the built-up membrane, modified bitumen membrane, single-ply membrane, low-sloped metal panel system, and Spray Polyurethane Foam system. Similar to other building systems, roof systems are very susceptible to failures. The most common are performance grade failures such as water and air intrusion. However, more serious failures such as up-lift and collapse occur all too often.
Performance FailuresLike all other systems in a building, roofs can fail. In fact, roofs account for the majority of necessary building repairs and building litigation cases in the United States. However, most of the failures that occur in a roof system are not major collapses, but simply performance failures. Although each roof system has its own specific failure modes, there are a variety of common performance failures that can result in necessary repairs. Some of these failures that require repair include the following:
- Blistering
- Splitting
- Punctures/ Penetrations
- Wrinkles
- Flashing Installation
- Surfacing
- Fasteners
- Shrinkage
- Ponding
- Leaks or moisture intrusion
- Abuse, neglect, and lack of maintenance
(Note: We’ve chosen to focus on Leaks or Moisture Intrusion as a topic related to mold growth and other problems.)
Leaks or Moisture Intrusion
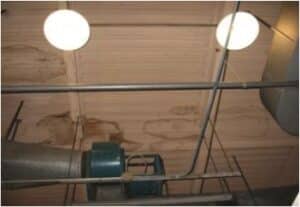
Moisture intrusion is the most critical performance failure that occurs in roof systems. If a roof system is leaking, it has completely failed in doing the job it was designed to do (see definition of roof system in Introduction). As already discussed in this report, all roof types are susceptible to leaks, and almost all other failures that have been mentioned can eventually lead to this failure. In addition to poor membrane and flashing installation/performance, other causes to moisture intrusion include poor drain details/ construction, rain during construction or uncovered repairs, poorly installed expansion joints, wind driven rain, and a multitude of other various issues. Leaky roofs are a huge problem in the building industry, causing billions of dollars each year in damage and repairs.
Water intrusion can ruin the integrity of the entire roof assembly, including the roof deck, insulation, and structure (it can even cause eventual collapse in certaincircumstances). Water intrusion into the interior of the building is also an issue. Water can ruin interior finishes, short electrical lines, cause staining, ruin storage or equipment, rot wood or rust metal,and cause microbial growth such as mold and become a health issue.Therefore, it is critical that roof systems are detailed/constructed to ensure water tightness, and all eventual water intrusion failures are quickly and properly repaired to prevent further problems. Approved test methods to ensure water tightness include common tests that have been used for a long time such as flood testing, as well as infrared, nuclear, impedance, high-voltage, and other testing that are newer to the industry.
Source: Michael Payne for Wikispaces; free to use as per Creative Commons.
Please contact Aspen Environmental Services for mold testing, mold removal, and flood damage repair at (978) 681-5023. Licensed and insured; member of NADCA, NORMI, and BBB. Or email [email protected]